
Voice-picking in warehouse
With the new voice-directed picking solution the time used for picking one customer order has been reduced by 50%.
Miika Heinonen, Logistics Director, Verkkokauppa.com
Cross-docking – Hectic Moments in Order Handling
The hectic atmosphere of a cross-docking terminal provides an environment where costly supply-chain errors can happen, and there Voice fits perfectly. Supplier delivers one pallet of a product. When the pallet arrives to cross-docking terminal, instead of entering the products into the warehouse, they are redirected to dispatch area, where they are divided to single deliveries to the right customers. Cross-docking is very hectic, batches are often large, and there can be dozens of pallets with thousands of separate customer orders. All deliveries have to be handled quickly and without errors. Voice is the perfect solution.
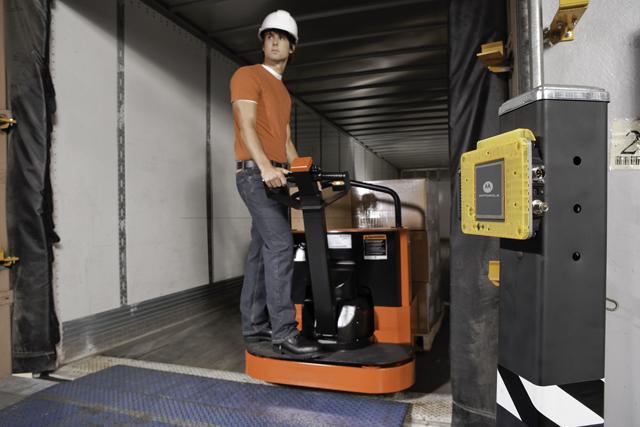
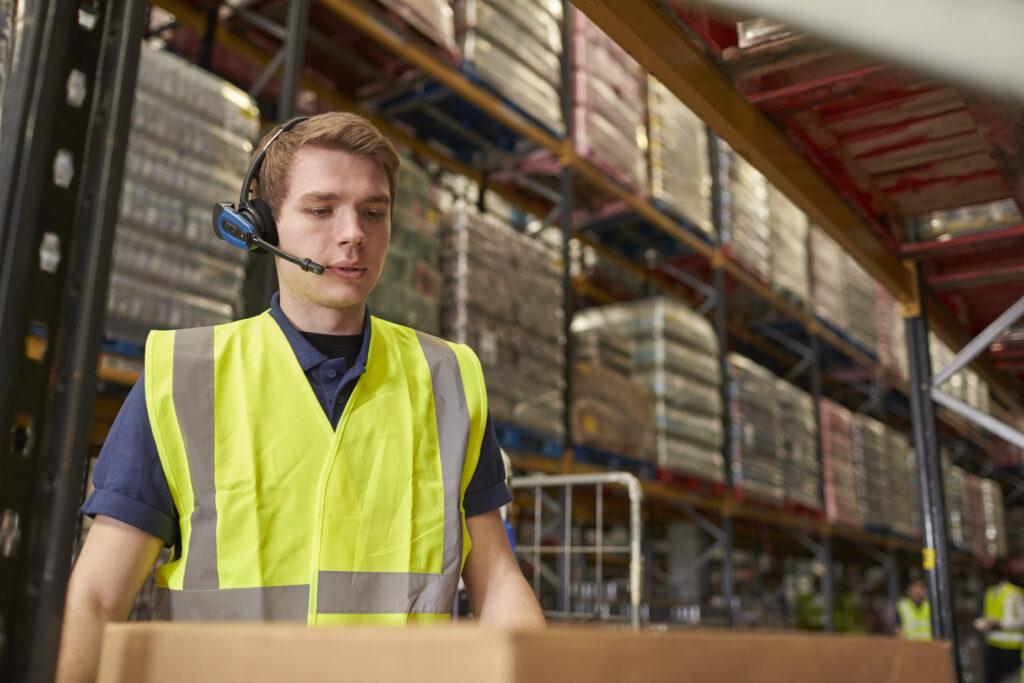
Batch picking enhances operations
Batch picking is one example of how voice enhances warehouse operations. Batch picking means picking several orders (to several customers) at the same time. The benefits can be seen when picking small orders with few order lines and small amounts. The picker can pick even over 50 orders at the same time. When picking to multiple customers at the same time, it is easy to make a mistake and add products to wrong pallet and then it will be delivered to a wrong customer. This problem is eliminated with the confirmation dialogue included to pick-by-voice. With batch picking it is also very easy to combine customer´s smaller orders into one bigger batch. By creating consolidated orders picking errors are eliminated and efficiency increased.
Picking list display brings optimum picking order
In a 3PL company the product range is usually very large varying from cement sacks to furniture, from crowbars to fluorescent lamps. And everything in between. Large scale of the products has inspired to develop a picking list display to support the pick-by-voice solution. With the help of the display the picker can pick the products in an optimized order so that bigger or heavier articles are picked to the bottom of the pallet and fragile and smaller products are placed on top of the pallet. The touch screen display is mounted on a forklift or a picking cart. On the display the picker can see all order lines and picks the big and bulky items first.
It is also possible to divide larger amounts of a product to several batches and place them on different pallets. From the screen the picker chooses the line he wants to divide, picks it partially and then later return to pick the rest when he has a new empty pallet. This enables the picker to balance larger batches on several pallets. Combining Voice with picking list display, you receive multiple benefits. Voice enables hands free – eyes free operation and picking list display allows the picker to use his professional knowledge to optimize the picking order. Pickers´ objective is to produce well packed pallets that endure the whole delivery route.
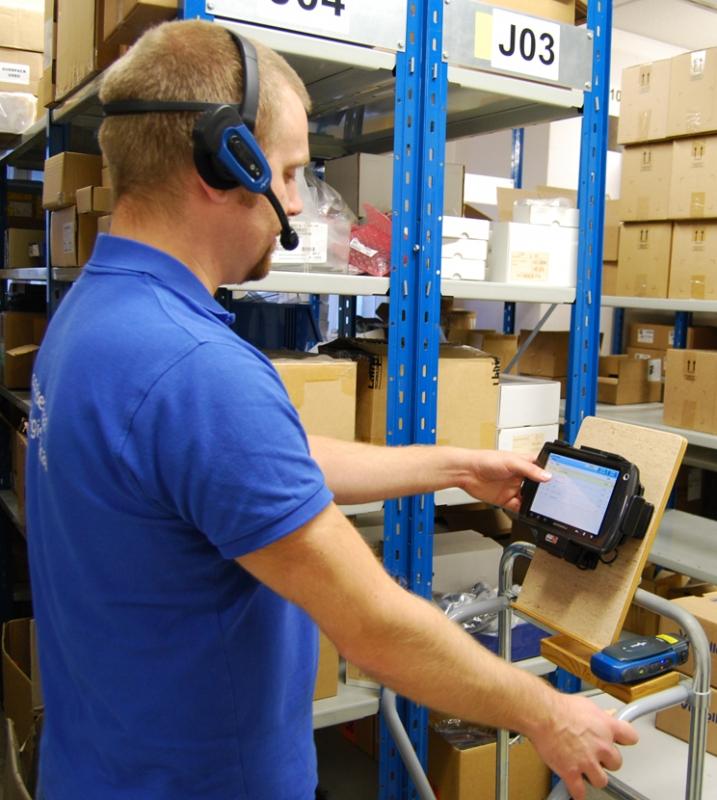
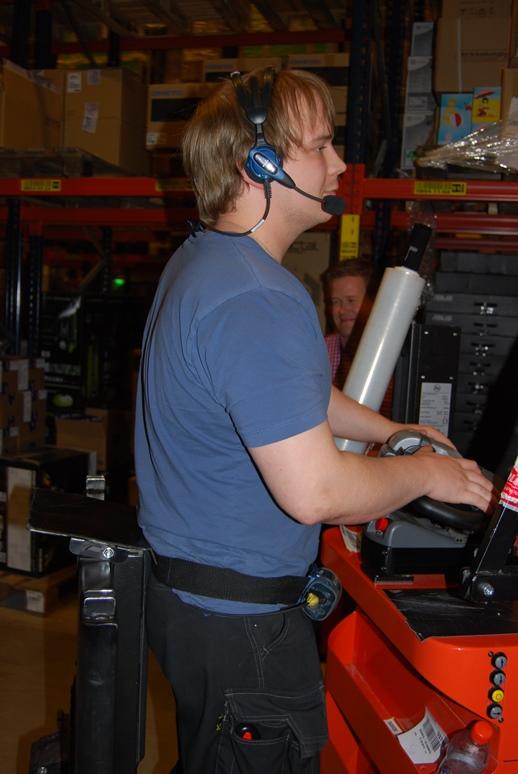
Read our case story: Voice-directed picking solution at Verkkokauppa.com
Verkkokauppa.com – has been a pioneer in designing multi-channel order-to-delivery process and successfully serving its customers for years.
“Since early times, we have been offering our products to customers through multiple channels, with the possibility to get the products delivered to their homes, offices or chosen pick-up points“, describes Henrik Weckström, CTO, Verkkokauppa.com.
“One distinct advantage of Pick-by-Voice provided by Vocollect is the possibility for batch picking or handling multiple orders at the same time. This means that the picker can pick up to 40 orders concurrently. Orders made on-line with the personal pick-up option are picked when customer arrives to the store. This sets up major demands for the picking system. All orders must be completed quickly and without errors.
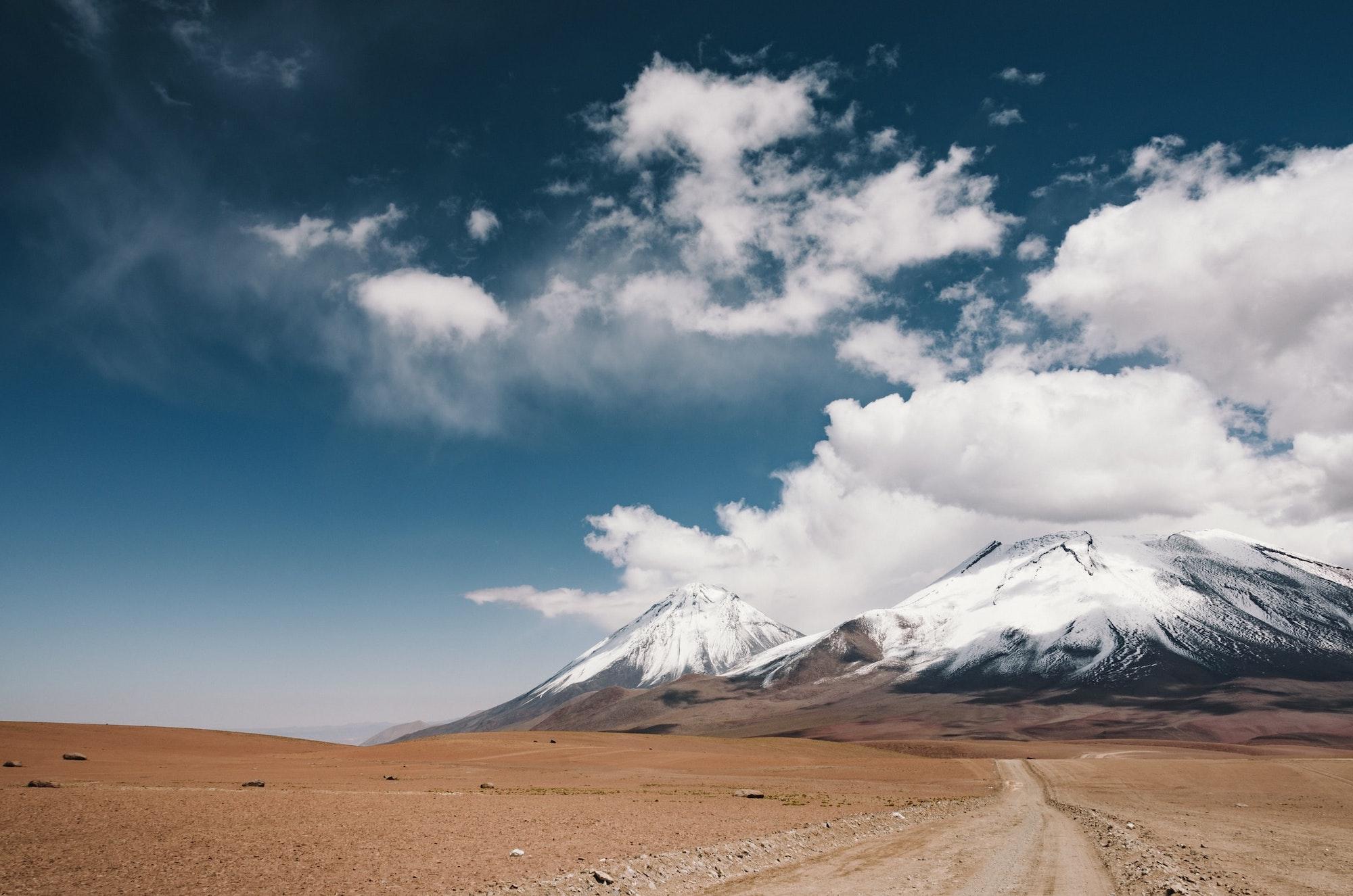
Major productivity improvement is delivered by picking multiple orders with several products at the same time. When using pick-by-voice the picker requests new orders by using a voice command and receives instructions on the location of the first product. The picker then reads the check digit identifying the storage location and receives the pick quantity. The picker responds with the number of products that have been put on the carrier. The procedure is repeated until the order is finished and moved to shipping.

Agile all-in-voice warehouse processes
Warehouse processes from inbound to outbound can be performed with voice control or/and handheld devices.

Shipping Accuracy
Easy-to-use mobility and voice control enables productivity improvements from 15% – 35% with 100% shipping accuracy.
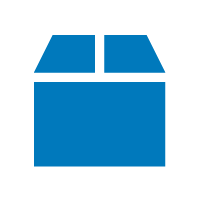
Easy to customize
The workflow can be easily configured to meet different business needs.

Process quality and efficiency
AbakusDirect improves the quality and efficiency of processes and lowers labor costs.