Reference story : Mediq Suomi Oy
Mediq Suomi Oy is the leading supplier of healthcare equipment, supplies and services in Finland, serving healthcare and laboratory professionals. Mediq selected Abakus, a Warehouse Execution Solution, as they wanted to improve and easily manage all warehouse operations from receiving and put-away to picking and dispatching.
A wide variety of healthcare articles and accessories from drop bottle holders to syringes and toilet paper is included in Mediq´s offering, excluding only medicines. Previously all orders were handled by means of a manual paper-based method that was very slow. Mediq replaced manual warehouse operations with Pick-by-Voice for picking and handheld scanners for receiving, including other warehouse processes. The new technology enables Mediq to offer their customers all necessary services under one roof – quickly and flawlessly.
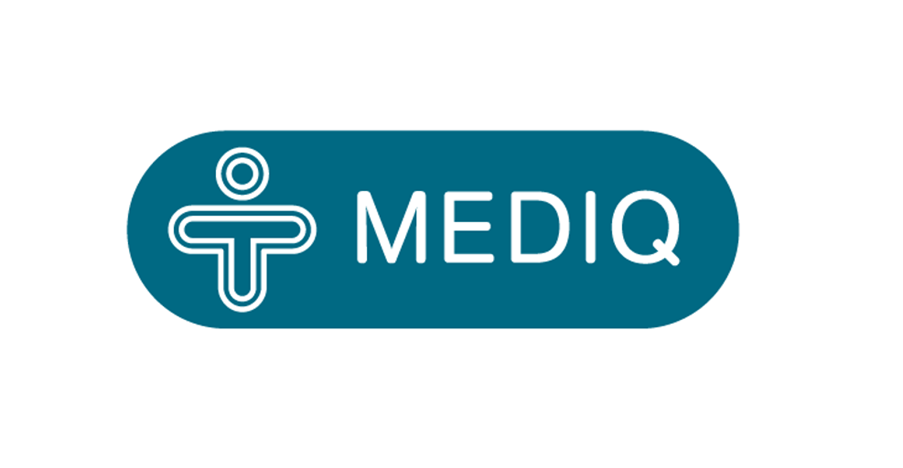
Abakus has increased our productivity and streamlined our processes, which is highly appreciated also by our customers. The delivery accuracy is now very high and improvement in managing deviations has kept reduced cost.
Satu Hallikainen, Warehouse Manager, Mediq Suomi Oy
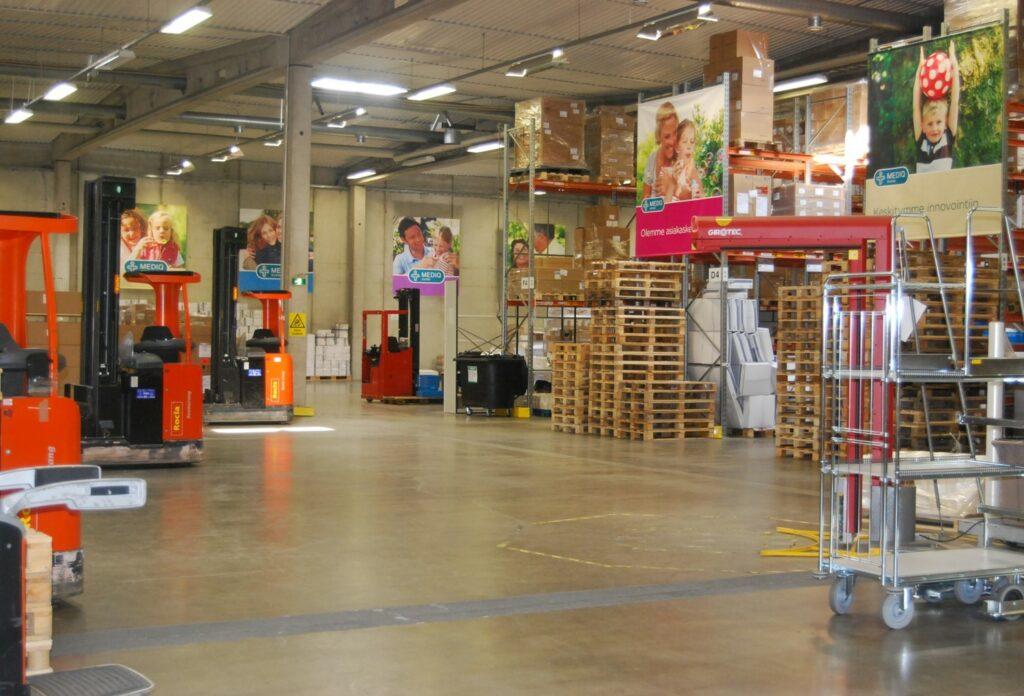
Management has real-time visibility to warehouse operations
There are numerous of transactions in Mediq warehouse: products are received, replenished and then picked according to customers´ orders. Mediq offers customers next-day delivery, which set high requirements on warehouse solutions. Deliveries and human resources are managed with a web interface included in the Abakus solution. Managers have a transparent, always up-to-the-minute view of all open tasks, which allows supervisors to manage/control operations at all times. They can reassign resources when an urgent delivery is due and needs extra hands, or when the reception area is full and more deliveries are about to be shipped in.
About 40% of the orders are one-line purchase orders. The Abakus system can easily enhance picking by consolidating many small orders to be picked at the same time. The pickers can also check the inventory or request replenishment whenever needed. Handling rules for every product and item location have also been defined in the Abakus solution. This enables supervisors to choose the most suitable picking method (Voice or handheld) according to the product measurements and weight.
Substantial amount of suppliers
Due to its wide product range, Mediq has many suppliers, which creates challenges as suppliers´ product-specific labeling varies considerably. One piece of a certain product can mean many things from a single item to a “family-size package” with 12 items.
One piece of a product can also mean both the bottom and the lid or just the bottom. All this variation increases the risk of errors. With Abakus, these challenges are a thing of the past. Reference and product codes as well as product descriptions are included in Abakus. The system also guides the warehouse operator to fill in the necessary product information such as batch numbers, best-before dates and product measurements when entering the item into the stock. This procedure ensures that the customer gets the right amount of the right product from the right batch.
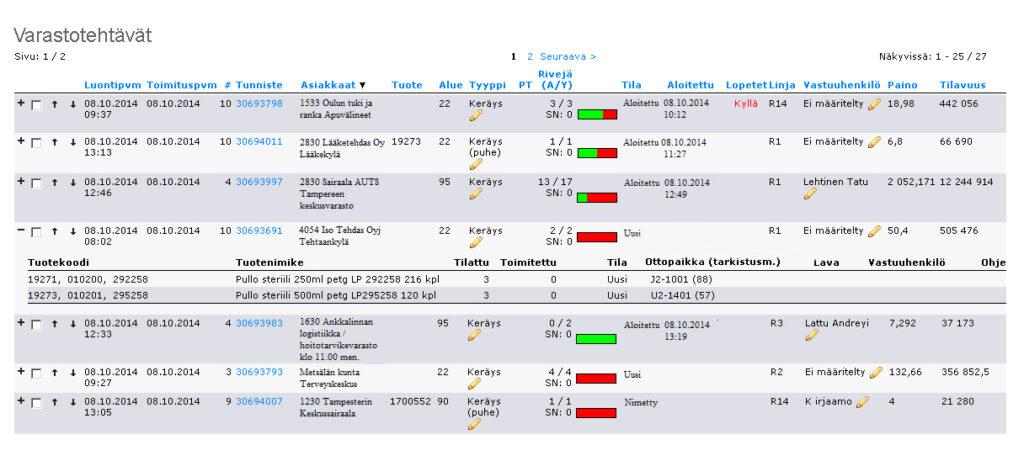